Automatic feed pushing robot
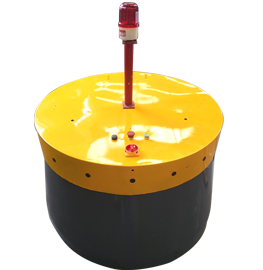


Product Video 
Advantages
- 24 hours work, saving manpower
- Increased roughage intake and more milk production
- Save costs and reduce waste
- Automatic charging, continuous battery life
- Trackless navigation, intelligent path planning
Intelligentfree cow traffic was born
Inthe process of feeding the cows, the feed will be pushed outside and away fromthe fence. This requires manual work to push the grass and feed into thebullpen in real time, otherwise it will reduce the feed intake and milk yieldof the cows, and cause a lot of waste of feed. In order to ensure that cowsreceive enough feeding at all times throughout the day, intelligent pushinggrass robots can be used instead of manual pushes for easy feeding.
Achieve uninterrupted feeding to save your effort
Intelligentpushing grass robot to improve feeding efficiency and improve the living conditionsof dairy cows, while less labor.
Itis well known that frequent feeding increases feed intake of cows and thusincreases milk production. In addition, high frequency feeding also has apositive effect on the health of dairy cows. In the dairy farm, the automationof the feeding process is a guarantee to further increase milk production,improve feed conversion efficiency, and less labor.
Intelligent free cow traffic working way
The intelligent grass pusher is driven by twodrive wheels and assisted by two driven wheels. It is powered by a battery,under the monitoring of the ultrasonic sensor to ensure that the intelligentpushing grass robot travels along the feeding fence according to a pre-setroute. It is automatic push and be able to push feed up to 45cm.The intelligentfree cow traffic is equipped with an obstacle detection device and will stopmoving immediately when encountering an obstacle in the process of driving. Itputting safety in the first place. After the end of the operation, it willreturn to the charging station for self-charging.
Specifications:
Equipment Diameter: 122cm
Height: 82.5cm
Weight: 530kg
Height of push plate : 60cm
Drive mode :Motor (2 pcs)
Number of wheels: 4pcs
Maximum travel speed: 12 m/min
Number of batteries :2pcs
Voltage: 48V
Battery capacity:60Ah
Feed maximum width :200cm
Maximum height of feed : 45cm
Full charge driving distance : 600M
Determination of direction of motion: Gyro locator and ultrasonic
Determination of the forward distance: Ultrasonic sensor
Path setting: Teaching manual mode